Injection Molding Service for Custom Parts
Discover our expert injection molding services for custom parts. Get free quotes and feedback to streamline your prototype and production tooling needs.
What Is Injection Molding?
Injection molding stands out as a highly efficient manufacturing process for creating plastic parts in large volumes. By injecting molten plastic into a custom mold, this method ensures each product maintains consistent quality and precision. The cost-effectiveness of injection molding is unmatched, as the initial expense of the mold is offset by the ability to produce thousands of units at minimal cost per piece. Furthermore, this process supports a vast range of materials, colors, and finishes, making it versatile for various applications and industries.
How Injection Molding Works
Injection molding is a widely used manufacturing process for producing plastic parts by injecting molten material into a mold. This process is essential in various industries due to its efficiency and ability to produce complex shapes with high precision. Understanding the injection molding cycle is crucial for optimizing production and ensuring the quality of the final product. The cycle consists of several key steps, including clamping, injection, cooling, and ejection, each playing a vital role in shaping the final product.
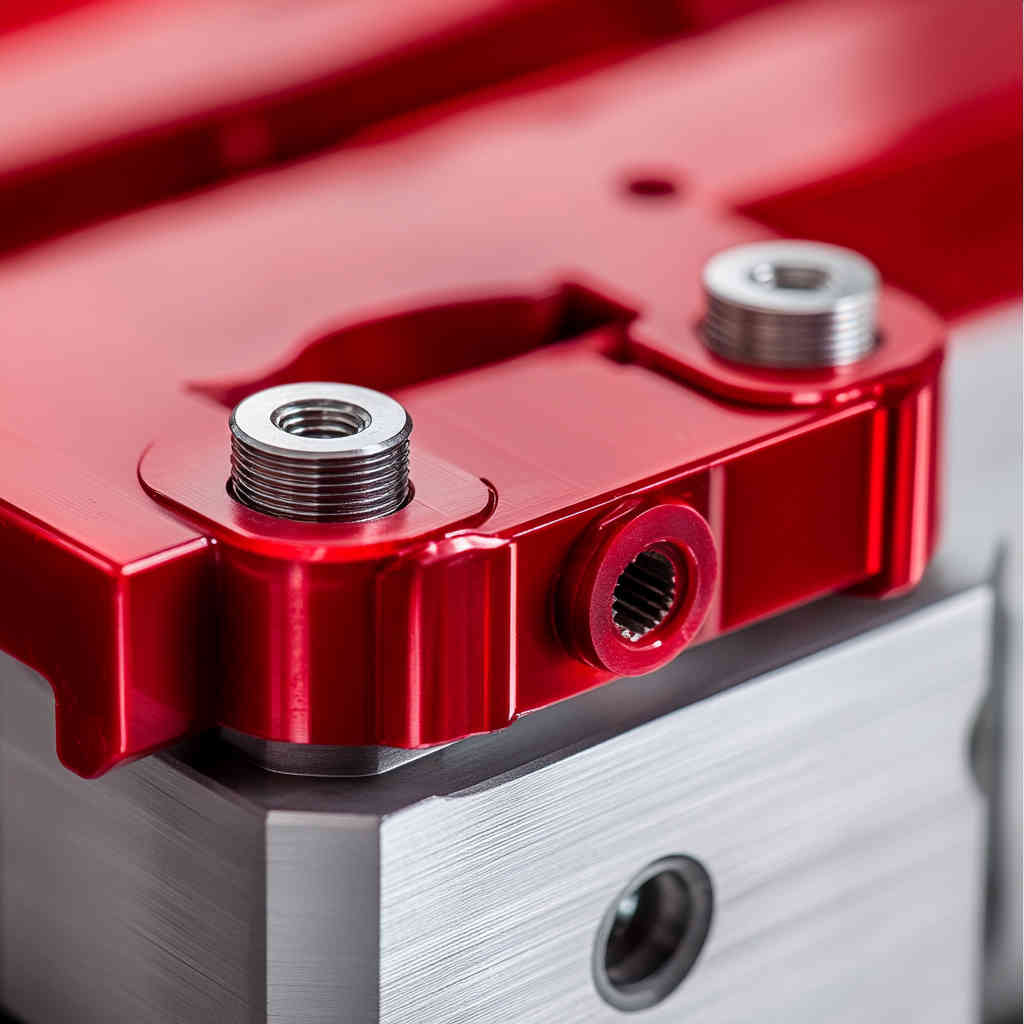
Clamping Process in Injection Molding
The clamping process is the initial step in the injection molding cycle, where the two halves of the mold are closed and held together under pressure. This ensures that the mold remains securely shut during the injection phase, preventing any material leakage. The clamping unit consists of a fixed and a moving platen, which work together to apply the necessary force. Proper clamping is crucial for maintaining the integrity of the mold and ensuring that the final product has a consistent shape and size.
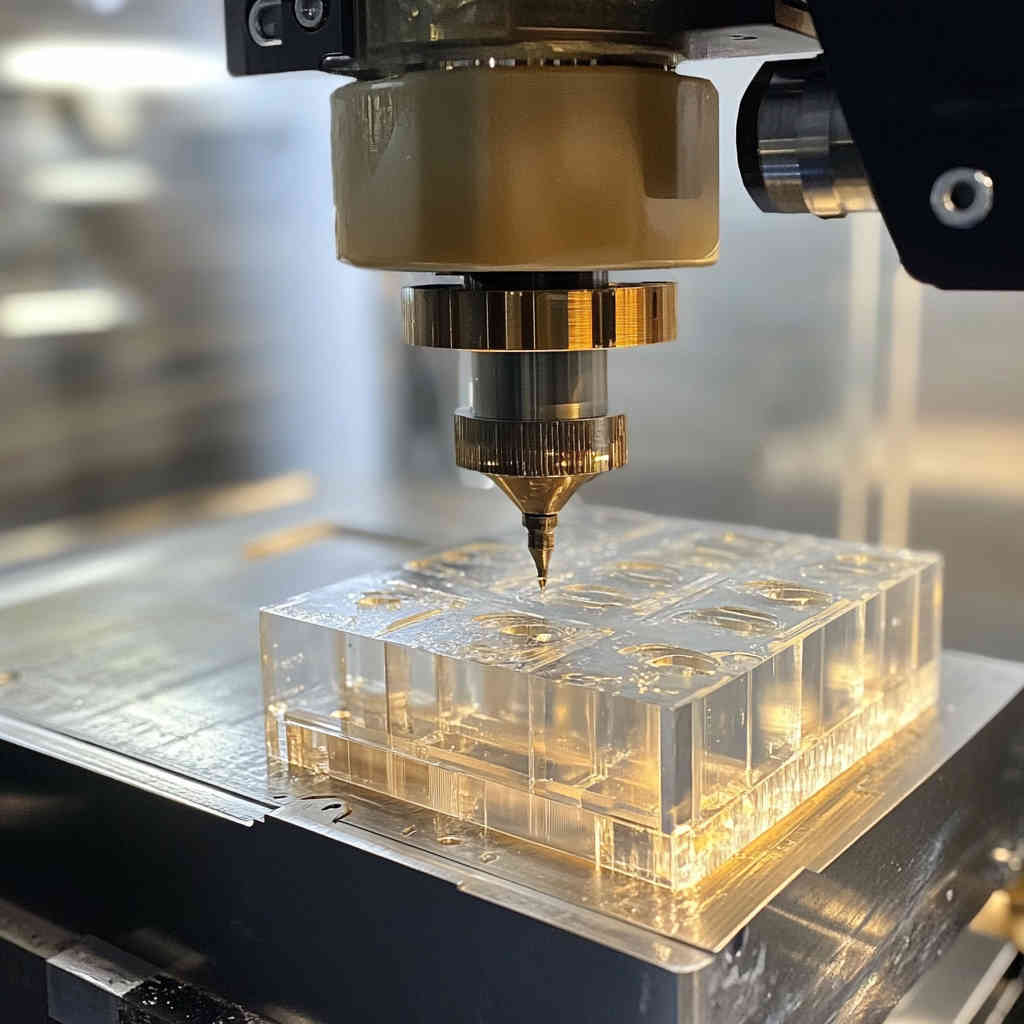
Injection Phase: Feeding and Melting
During the injection phase, raw plastic material is fed into the injection molding machine, where it is heated and melted. The molten plastic is then pushed into the mold cavity under high pressure. This step, known as the "shot," is critical for shaping the plastic into the desired form. The precision of the injection process determines the quality of the final product, making it essential to control the temperature and pressure accurately.
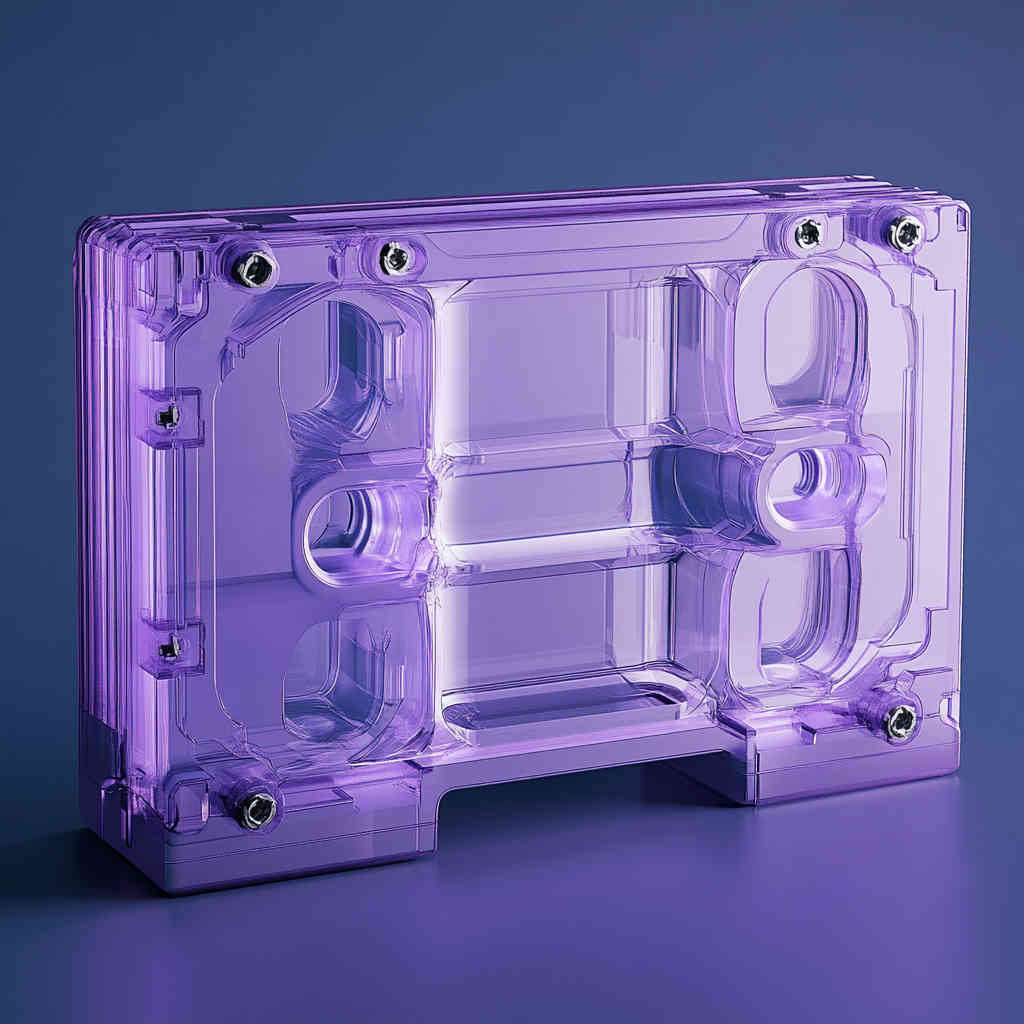
Cooling Stage: Solidifying the Part
After the plastic has been injected into the mold, it enters the cooling stage. During this phase, the plastic solidifies and takes on the shape of the mold cavity. Cooling time is a critical factor in the injection molding cycle, as it affects the overall production speed and quality of the part. Efficient cooling systems are essential to ensure that the part is evenly solidified, reducing the risk of defects such as warping or shrinkage.
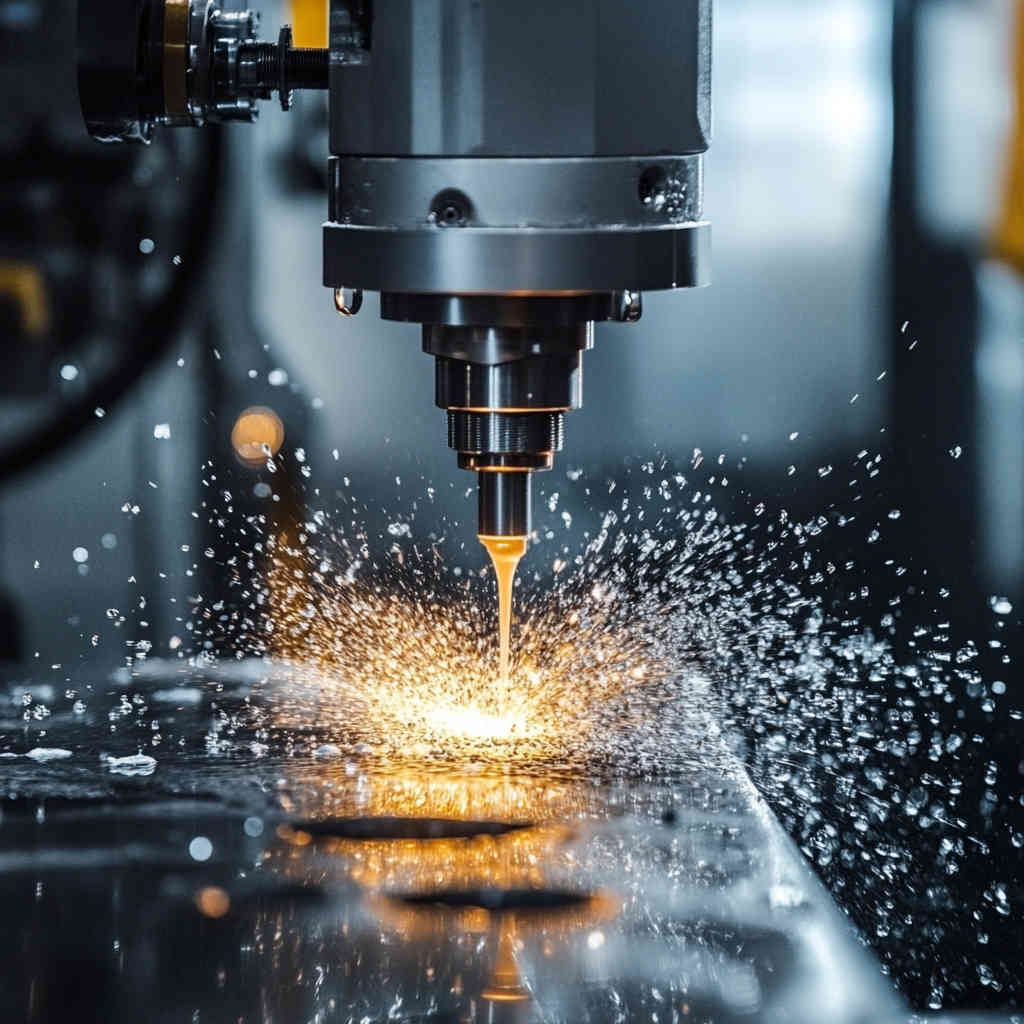
Ejection: Releasing the Finished Part
The final step in the injection molding cycle is the ejection of the cooled and solidified part from the mold. This is achieved using an ejection system that gently pushes the part out of the mold cavity. Proper ejection is crucial to prevent damage to the part and ensure its surface finish is not compromised. Once ejected, the part is ready for any necessary post-processing or assembly, marking the completion of the injection molding cycle.
Gallery of Our Injection Molded Products
Discover our diverse range of precision-engineered injection molded products, showcasing the capabilities and craftsmanship of our advanced manufacturing process. From intricate components to robust industrial parts, each product is designed to meet the highest quality standards, ensuring durability and performance. Explore our gallery to see the versatility and innovation that our injection molding solutions can bring to your projects.
The Process of Our Injection Molding Service
Discover the streamlined process of our injection molding service, designed to ensure precision and efficiency at every stage. From uploading your design to reordering parts, our comprehensive service guarantees high-quality results tailored to your needs. Experience seamless collaboration with our technical team and manufacturing partners as we guide you through each step, from design review to final delivery.
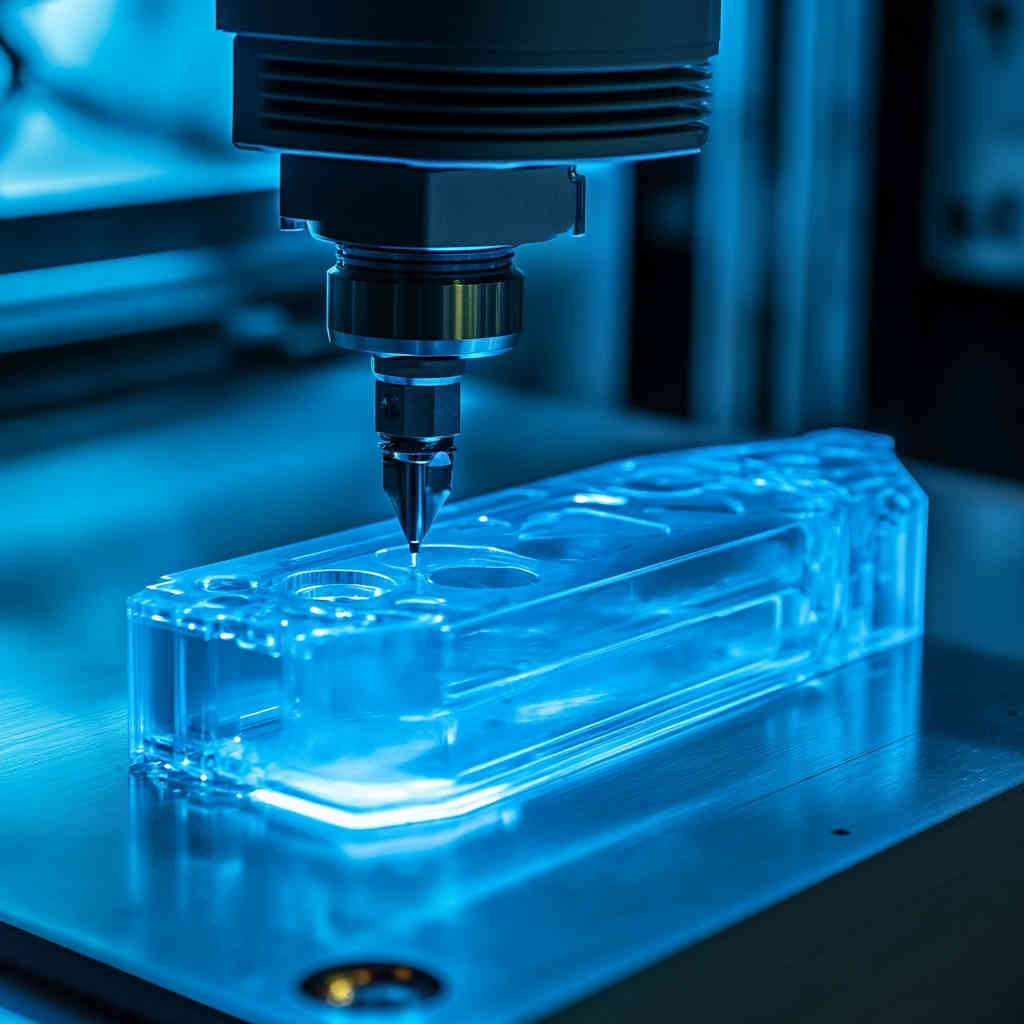
Upload Your Design for Injection Molding
Begin your injection molding journey by uploading your parts design to our user-friendly platform. Our expert team will meticulously review your project to ensure it meets the necessary criteria for successful manufacturing. This initial step is crucial for identifying any potential issues early on, allowing for efficient adjustments and optimal results. Trust our experienced professionals to guide you through the process with precision and care.
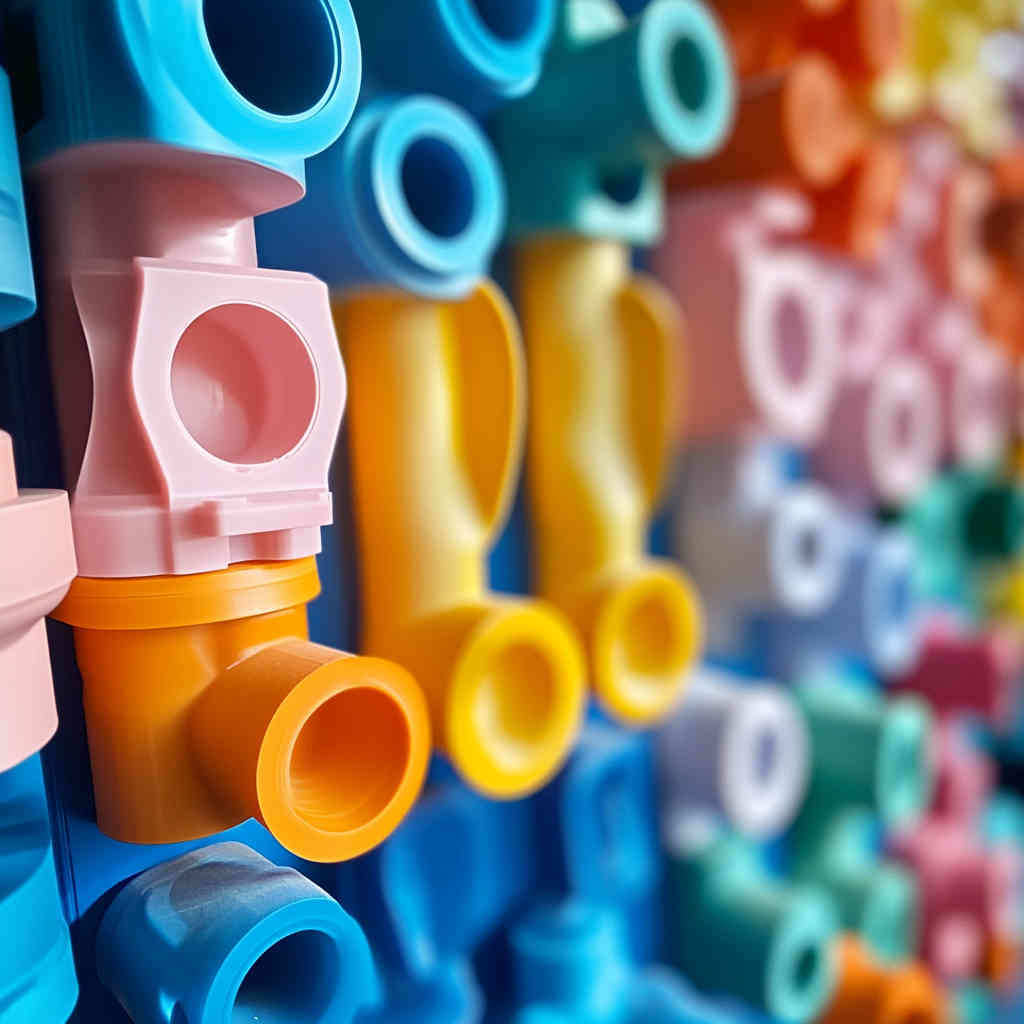
Receive a Comprehensive Quote in 48 Hours
Within just 48 hours, receive a detailed quote tailored to your project's specifications. Your dedicated account manager collaborates closely with our technical team and manufacturing partners to ensure that every aspect of your design is considered. This collaborative approach guarantees transparency and accuracy, providing you with a clear understanding of costs and timelines, empowering you to make informed decisions.
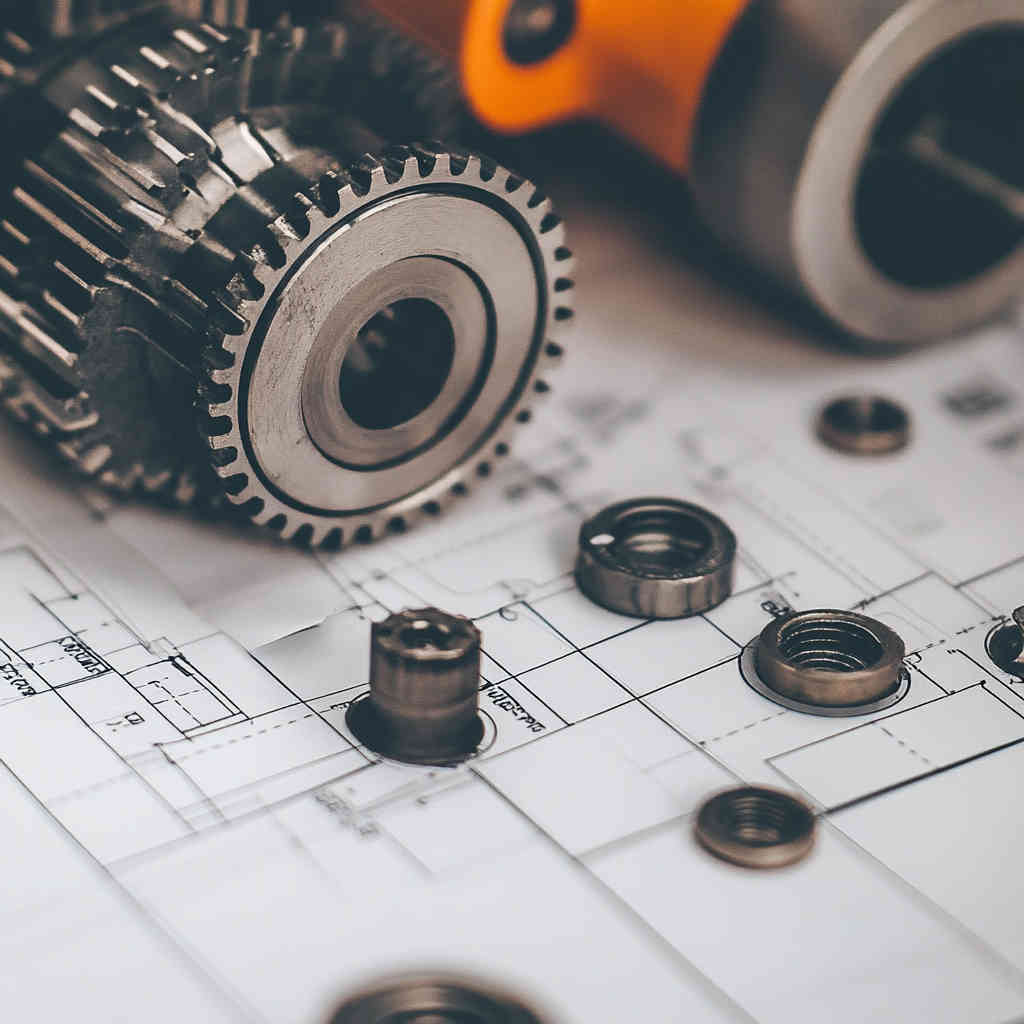
Design For Manufacturing (DFM) & Tool Approval
Receive an in-depth Design For Manufacturing (DFM) analysis to refine and perfect your design before tool construction begins. Our team of experts will provide insights and recommendations to enhance manufacturability and efficiency. Approving the DFM ensures your tool is built to the highest standards, minimizing risks and optimizing production outcomes. Partner with us for a seamless transition from design to tool creation.
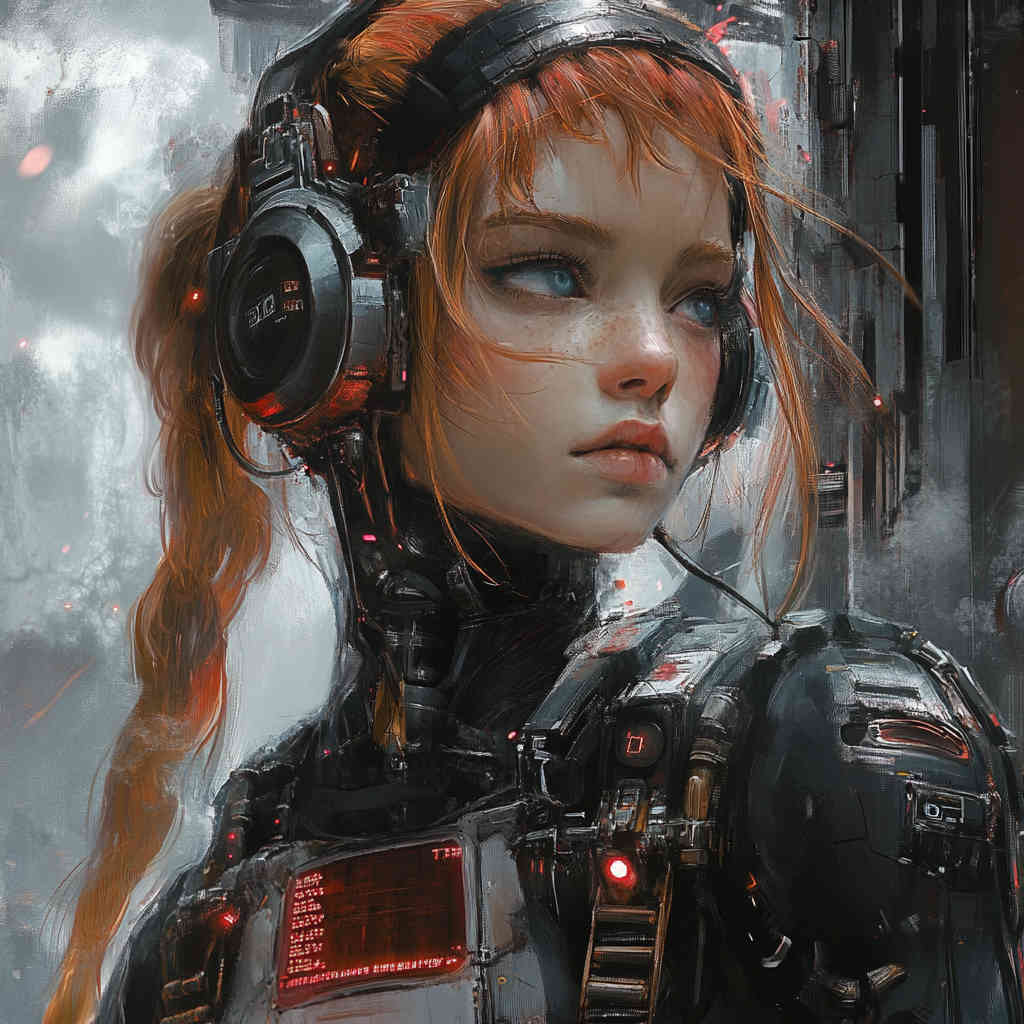
Approve T1 Samples Before Full Production
Before full-scale production, we send you a T1 golden sample for approval. This critical step allows you to assess the quality and precision of the molded part, ensuring it meets your expectations and requirements. By approving the T1 sample, you confirm that the production process aligns with your standards, paving the way for consistent quality in the final product. Experience peace of mind with our meticulous attention to detail.
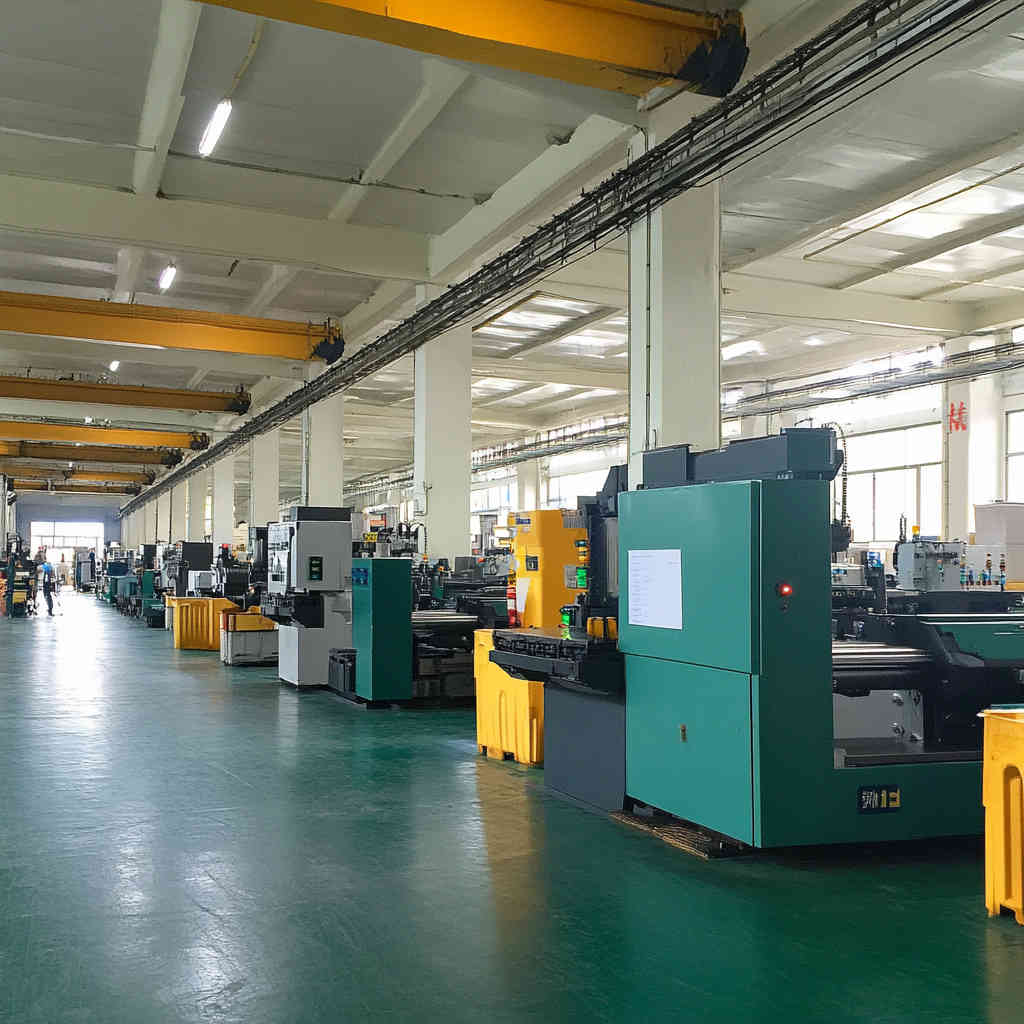
Efficient Production and Timely Delivery
Once the T1 sample is approved, we commence production to replicate the high standards of the golden sample. Our state-of-the-art facilities and skilled workforce ensure that each part is produced with precision and consistency. Upon completion, we manage the logistics to deliver your parts promptly, maintaining the integrity and quality of your order. Rely on our expertise for a smooth and efficient production process.
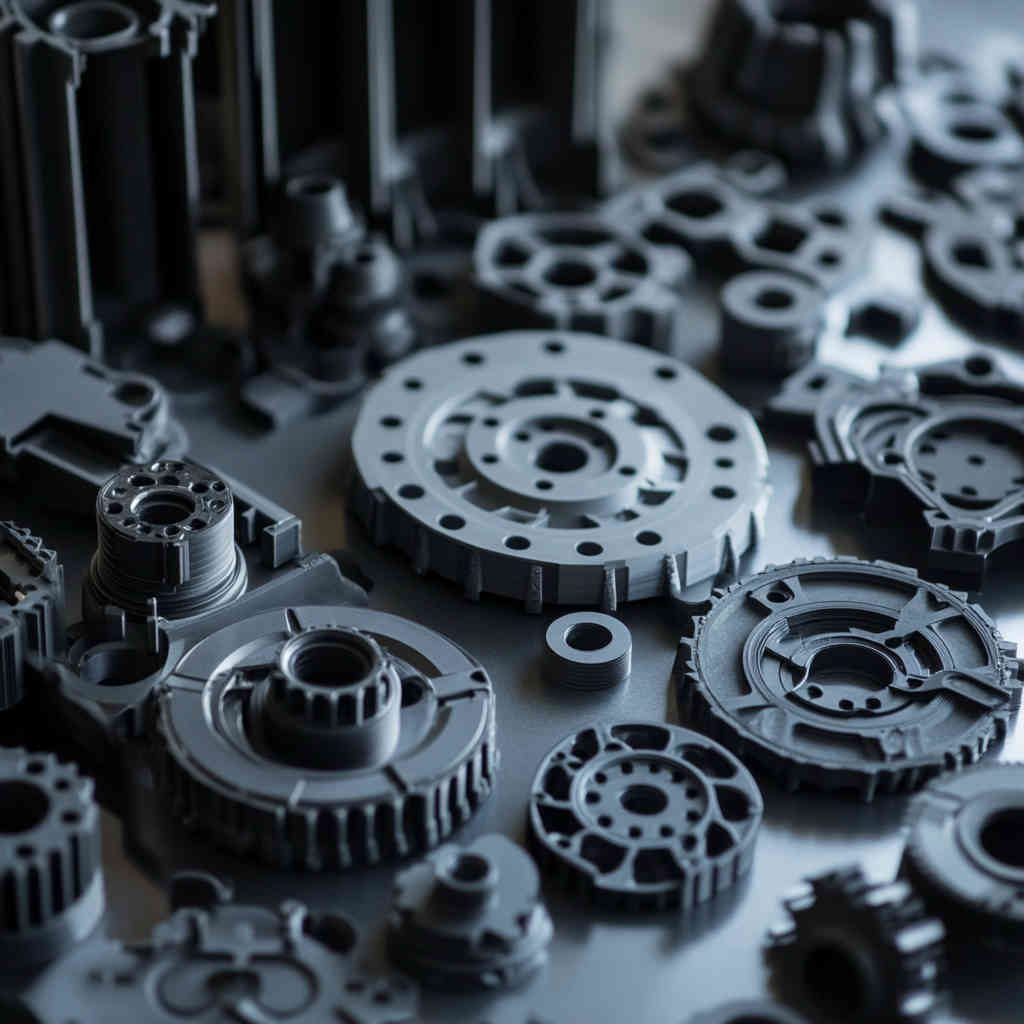
Convenient Reordering for Ongoing Projects
Simplify your supply chain with our convenient reordering process. Whether you need additional parts or ongoing production, your account manager is ready to assist with seamless reordering. This ensures continuity and consistency for your projects, allowing you to focus on your core business activities. Benefit from our commitment to customer satisfaction and long-term partnerships, ensuring your needs are met efficiently and effectively.
Looking for Injection Molding and Parts?
Reach out to us for expert guidance on your injection molding and parts needs. Our team is ready to assist with tooling validation and bridge production, ensuring your designs are realized with precision. Contact us today to discuss your project requirements and discover how we can support your manufacturing goals.
Injection Molding Materials
Property | Materials |
---|---|
Impact resistant | ABS, PMMA, PVC, PE, PC |
Wear-resistant | POM, PEEK, UHMW |
Dimensional stability | ABS, PBT, HIPS, PPS |
Chemical resistance | PEEK, PP, PBT, PE, LDPE, PA |
Rubber like | TPU, TPE, Silicone |
Cost-efficient | PP, HDPE, LDPE |
Cosmetic | ABS, PC, HIPS |
Injection Molding Finishing Options
Standard Finish Options
Our standard finish options provide a smooth and polished surface, ideal for products requiring a clean and refined appearance. These finishes are perfect for applications where aesthetics are crucial, offering a cost-effective solution without compromising on quality.
MoldTech Finishes for Enhanced Texturing
MoldTech finishes deliver intricate texturing, adding depth and character to your products. This advanced mold texturing technique enhances grip and visual appeal, making it suitable for consumer electronics, automotive parts, and more.
As Molded Surface Quality
The 'As Molded' finish captures the natural texture of the molded part without additional processing. This option is ideal for projects where cost-efficiency and maintaining inherent material properties are priorities.
Precision with Threaded Inserts
Incorporate threaded inserts into your injection molded parts for enhanced functionality and assembly ease. This feature ensures robust and reliable connections, suitable for products requiring frequent assembly and disassembly.
Additional Molding Options Available at GreeDaikin
At GreeDaikin, we offer an extensive range of additional molding options to cater to diverse industry needs. Our services include stamping molds and precision parts, designed to enhance manufacturing efficiency and product quality. With a focus on innovation and precision, GreeDaikin ensures that each solution is tailored to meet specific requirements, providing reliable and efficient results for your business.
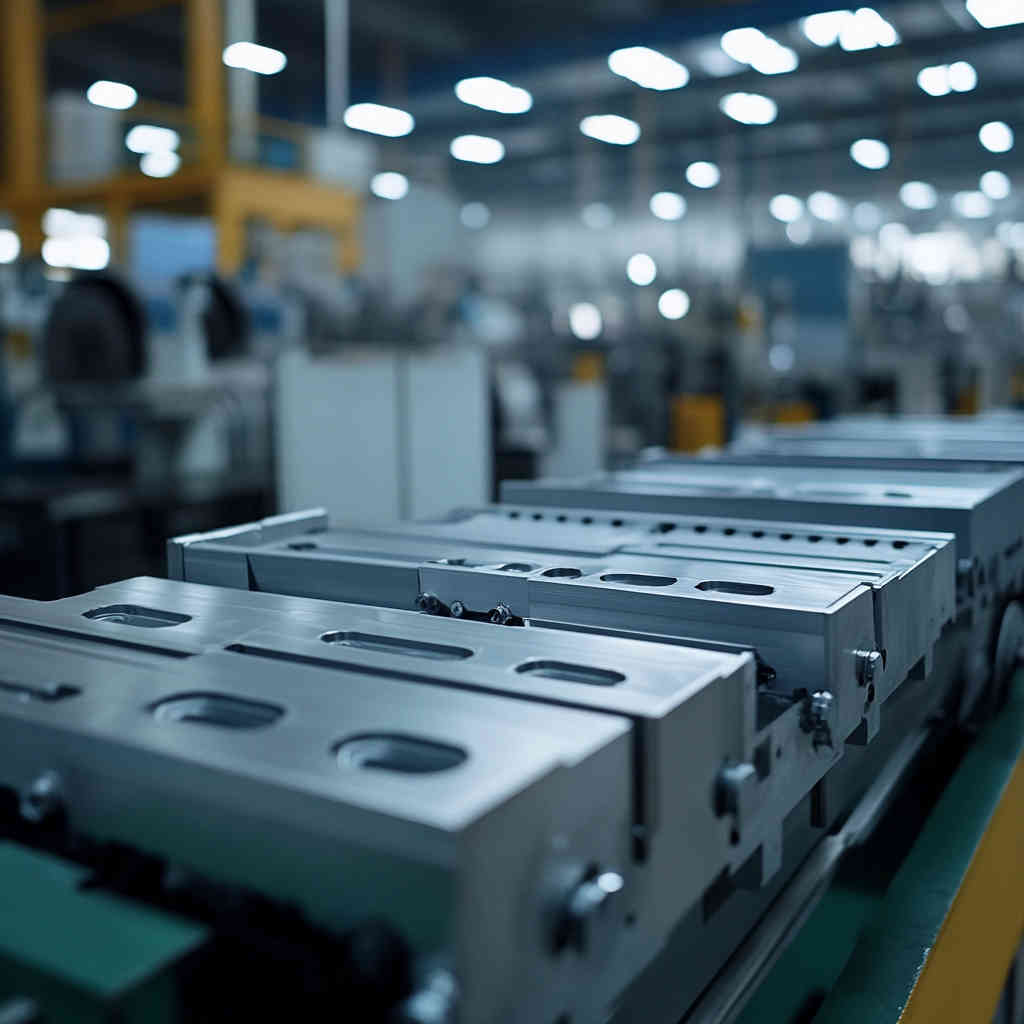
High-Quality Stamping Mold Solutions
GreeDaikin's stamping molds are crafted with precision to ensure durability and efficiency in production processes. Our molds are designed to withstand high pressure and repetitive use, making them ideal for large-scale manufacturing. We utilize cutting-edge technology and materials to deliver molds that meet the highest industry standards, ensuring that your products are consistent and of superior quality. Trust GreeDaikin for your stamping mold needs and experience seamless production with minimal downtime.
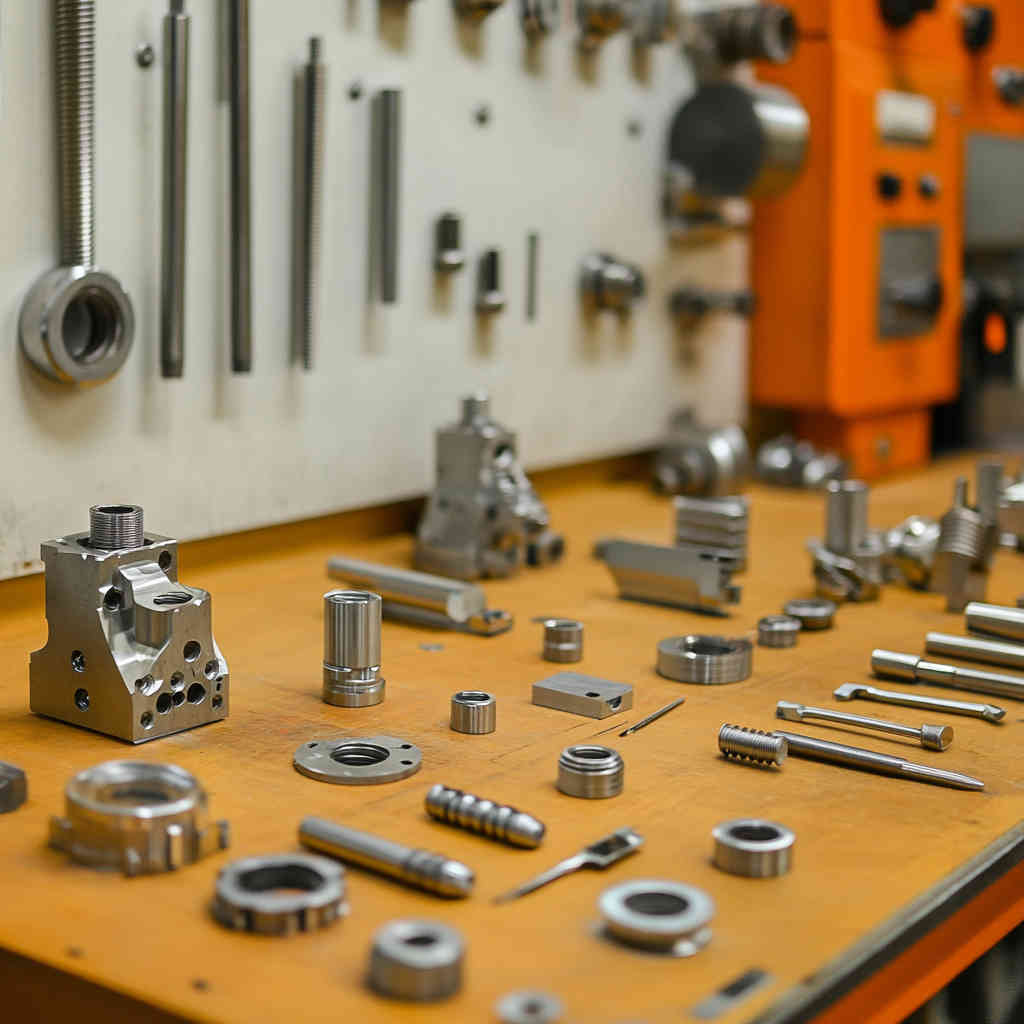
Precision Parts for Enhanced Performance
Our precision parts are engineered to provide exceptional accuracy and reliability for various applications. At GreeDaikin, we understand the importance of precision in manufacturing, which is why our parts are meticulously crafted to meet your exact specifications. Whether you're in aerospace, automotive, or electronics, our precision parts are designed to enhance the performance and longevity of your products. Choose GreeDaikin for precision parts that deliver unmatched accuracy and dependability.
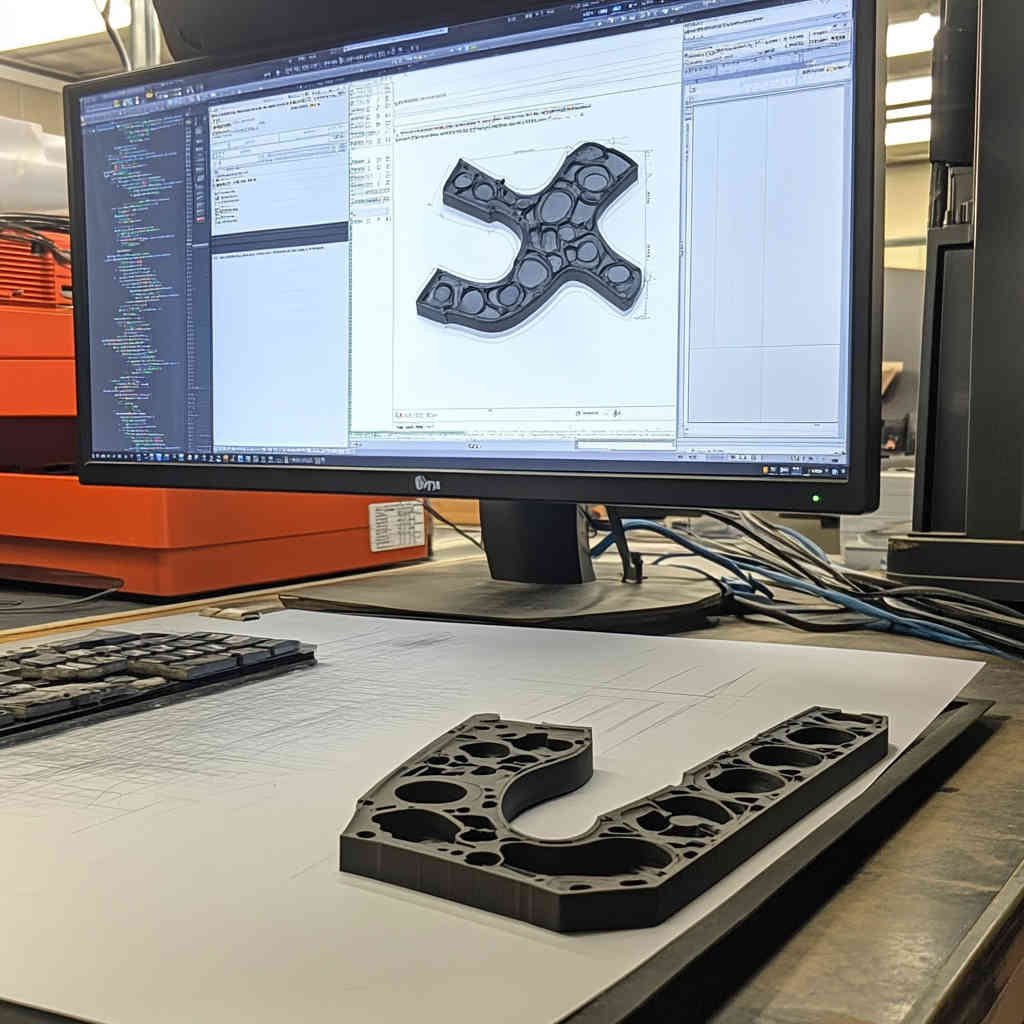
Custom Molding Solutions Tailored to Your Needs
At GreeDaikin, we offer custom molding solutions that are tailored to meet the unique requirements of your business. Our team of experts works closely with you to understand your specific needs and develop molds that enhance your production capabilities. From concept to completion, we ensure that every mold is crafted with precision and care, providing you with solutions that are both innovative and effective. Trust GreeDaikin for custom molding solutions that drive your business forward.
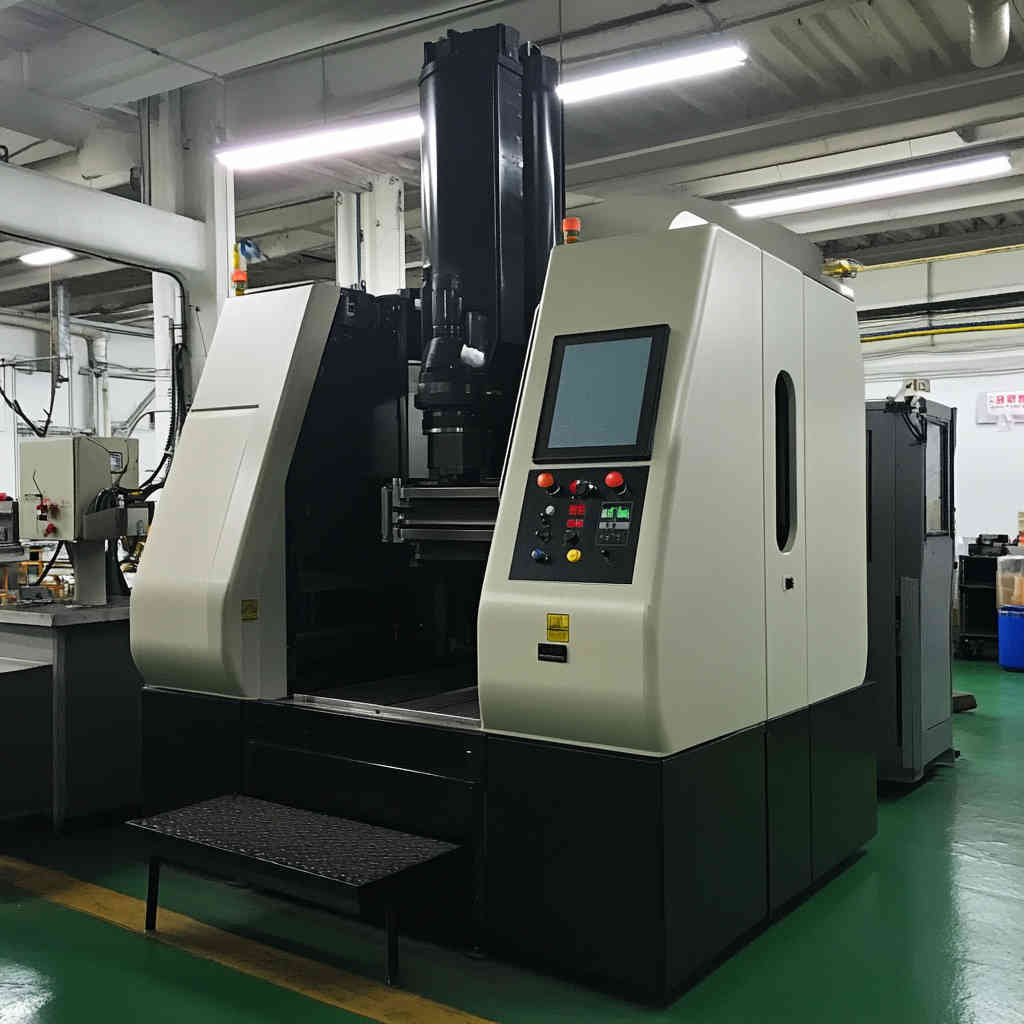
Innovative Technology in Mold Manufacturing
GreeDaikin is at the forefront of mold manufacturing technology, utilizing the latest advancements to deliver superior products. Our state-of-the-art facilities are equipped with advanced machinery and tools that allow us to produce molds with unparalleled precision and efficiency. We are committed to innovation and continuous improvement, ensuring that our clients receive the best possible solutions for their molding needs. Partner with GreeDaikin and benefit from cutting-edge technology in mold manufacturing.
Injection Molding FAQs
Injection molding is widely used across various industries due to its versatility and efficiency. Key sectors include automotive, where it helps manufacture parts like dashboards and bumpers; consumer electronics for creating durable housing and components; medical for producing sterile and precise equipment; and packaging for creating containers and closures. Additionally, the toy and household goods industries benefit from its ability to produce complex shapes with high precision. This diversity highlights the adaptability of injection molding for different applications.
Molding and printing are distinct manufacturing processes with unique applications. Molding involves shaping materials, typically plastics, into desired forms using molds, making it ideal for mass production of complex parts. In contrast, printing, particularly 3D printing, builds objects layer by layer, offering flexibility for prototyping and small-scale production. While molding is cost-effective for large volumes, printing allows for customization and rapid iteration. Understanding these differences helps select the right process for specific project needs.
After placing an injection molding order, the process involves several key steps to ensure quality and precision. Initially, design verification is conducted to confirm specifications. This is followed by tool creation, where molds are crafted to exact dimensions. Next, a trial run is performed to test and refine the mold. Once approved, full-scale production begins, with ongoing quality checks to maintain standards. Finally, the finished products are packaged and shipped to the client, ensuring timely delivery.
Ownership of the injection molding tool typically depends on the agreement between the manufacturer and the client. In many cases, the client owns the tool, especially if they have invested in its creation for exclusive use. However, some manufacturers may retain ownership if they provide the tooling as part of their service. It's crucial to clarify ownership terms in the contract to avoid misunderstandings and ensure both parties' interests are protected.
Yes, running different colors of the same material in injection molding is possible and commonly practiced. This is achieved by using colorants or masterbatches, which are added to the base material before molding. The process involves careful calibration to ensure consistent color distribution and quality. While changing colors can be efficient, it may require additional setup time and costs, particularly if frequent color changes are needed. This flexibility allows for diverse product offerings in various hues.
More Resources for Injection Molding
Explore comprehensive insights on injection molding, from understanding its mechanisms to mastering part design. Delve into detailed guides and expert tips to enhance your knowledge and optimize your designs for superior results in injection molding technology.
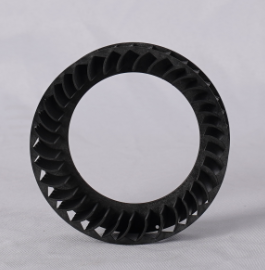
Injection molding material selection guide
2025-01-10
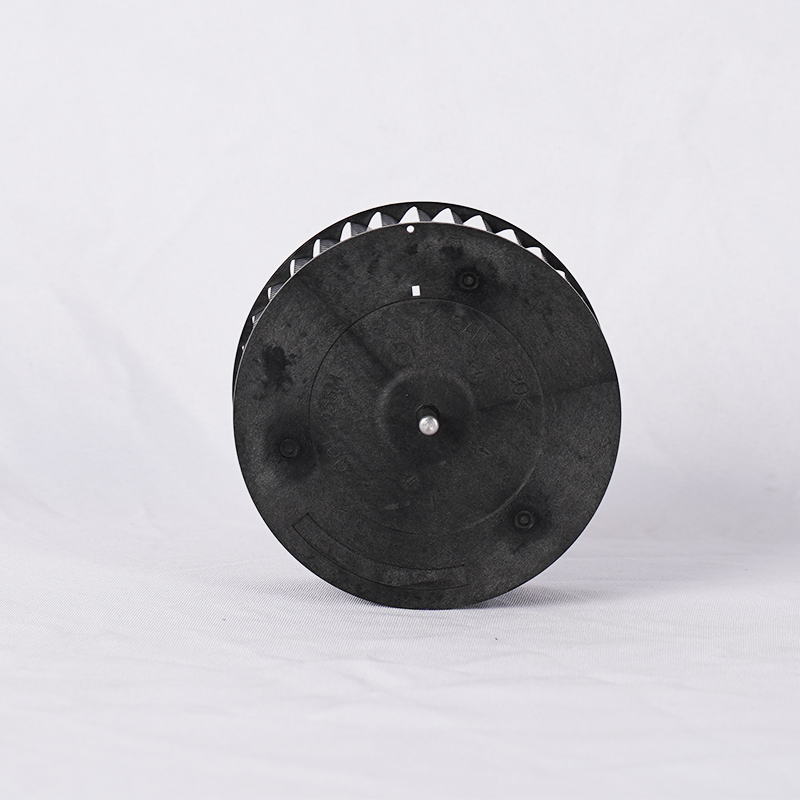
Which products require injection molding?
2025-01-16
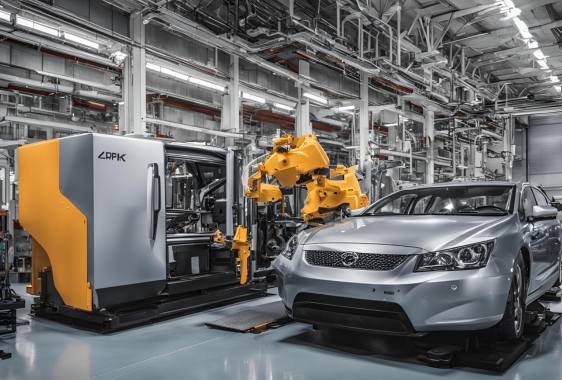
Is Injection Molding 3D Printing?
2024-12-06
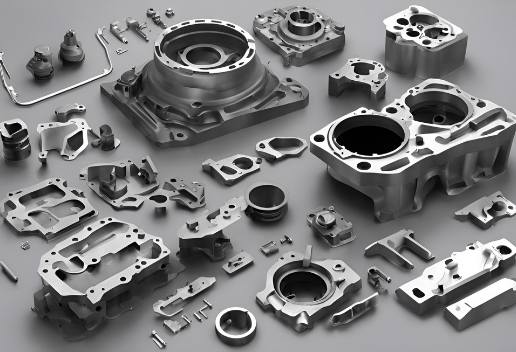
What Are Injection Molds Used For?
2024-12-10